Gravity casting is a metal casting process that involves pouring molten metal from a crucible into a reusable mold, relying solely on gravity without the aid of pressurized gas, vacuum or centrifugal force.
Aluminum Gravity Casting in Innovaw
Innovaw’s gravity die casting production line has 12 advanced tilting gravity die casting machines, including sand mixers, molding machines, pouring machines, and post-processing equipment.
Our gravity casting products cover automotive parts, medical devices, aerospace, lighting equipment, energy equipment components, marine vessels, industrial equipment, kitchen appliances and other components. The product sizes range from 100x100mm to 600x600mm, weights range from 100g to 50Kg, and daily production capacity is 3-4 tons.
Material Scope:
Aluminum:
ASTM-A319, A413, A355, A356, A357
JIS-AC2B, AC4D, AC4C, AC3A, AC4A
DIN-AlSi7cu4, AlSi5cu1Mg, AlSi7Mg, AlSi12, AlSi9Mg, AlSi12Cu2Mg1, AlSi6Cu4
ENAC-45000, 45300, 42100, 44100, 43300
In order to better provide one-stop service to our customers, Innovaw continues to maintain a high level of investment in research and development in the field of gravity casting. We have product development engineers and process experts who specialize in gravity casting.
We will continue to introduce the industry's advanced gravity casting equipment.
We continue to improve the details of the gravity casting process in practice, the pursuit of each and every bit of progress.
We continue to study the material properties and the best application of different materials in the field of gravity casting.
What Is Gravity Casting?
Gravity casting is a metal casting process that involves pouring molten metal from a crucible into a reusable mold, relying solely on gravity without the aid of pressurized gas, vacuum or centrifugal force.
1. Overview of the process
In gravity casting, the process of pouring molten metal into a reusable mold or die, where the molten metal flows from top to bottom under the force of gravity and flows to fill a designated model cavity, cooling and solidifying into shape. Molds are usually made of durable materials that can withstand high temperatures and reuse. The most common technique used in this process is tilt pour casting.
The process flow of low pressure casting includes the following major steps:
- Preparation of the Mold: The first step involves preparing the mold, which can be made from various materials, including metal or sand. The mold is often pre-heated to ensure better flow of the molten metal and to reduce the risk of thermal shock.
- Melting the Metal: The metal is melted in a crucible or furnace until it reaches a liquid state.
- Pouring the Molten Metal: Once the metal is ready, it is poured into the mold. This is done by tilting the ladle or using a pouring basin to direct the flow. The molten metal fills the mold cavity under the force of gravity, which helps minimize turbulence and oxidation, leading to better quality castings .
- Cooling and Solidification: After the mold is filled, the molten metal is allowed to cool and solidify. The cooling rate can affect the properties of the final casting, so it is important to manage this process carefully.
- Removing the Casting: Once the metal has solidified, the mold is opened, and the casting is removed. Any excess material is trimmed away.
2. Advantages of Gravity Casting
The Gravity Casting process offers several advantages:
- High Dimensional Accuracy: The gravity casting process is known for producing parts with exceptional dimensional accuracy. This precision is crucial for applications where tight tolerances are required.
- Good Surface Finish: Castings produced through gravity casting typically exhibit smoother surfaces compared to other methods.
- Superior Mechanical Properties: The process results in reduced porosity in the final products, which enhances their mechanical properties.
- Simplicity of Equipment: Gravity casting requires relatively simple equipment compared to pressure die casting methods. This simplicity allows for its use in traditional and low-tech foundry environments, making it accessible for various manufacturers.
- Cost-Effectiveness: While there may be higher initial tooling costs, gravity casting can be more economical for small to medium production runs due to the reusability of molds.
3. Applications of Gravity Casting
Gravity casting is widely utilized across various industries due to its ability to produce high-quality metal components with good dimensional accuracy and surface finish. Here are some key applications:
- Automotive Industry: Gravity casting is extensively used to manufacture components such as gearbox cases, engine blocks, and various structural parts. The process allows for the production of lightweight yet strong components, which are essential for modern vehicles.
- Aerospace Components: In the aerospace sector, gravity casting is employed to create parts that require high strength-to-weight ratios and excellent mechanical properties. Components like brackets, housings, and structural elements are commonly produced using this method.
- Consumer Goods: Many everyday products, including kitchen appliances and electronic enclosures, are made using gravity casting.
- Industrial Equipment: Gravity casting is also used to manufacture parts for industrial machinery, such as pump housings, gears, and other components that require durability and precision.
- Medical Devices: In the medical field, gravity casting is utilized to create surgical instruments and other medical devices that require high precision and reliability. The quality of the castings is critical in ensuring the safety and effectiveness of these tools.
- Lighting Fixtures: The process is often used to produce decorative and functional components for lighting fixtures. Gravity casting allows for the creation of detailed designs that enhance both the aesthetic and functional aspects of lighting products.
Application Industry
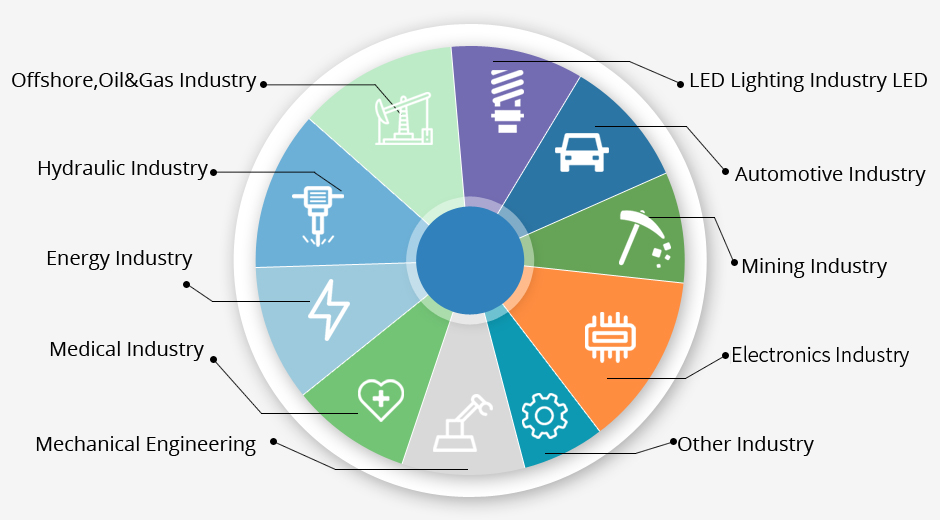
Partner
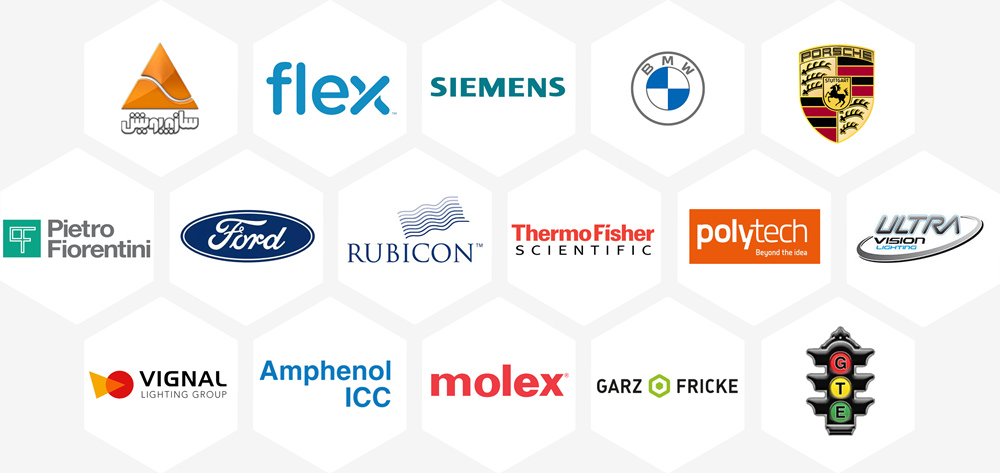