Investment casting, also known as lost wax casting, is one of the most diverse casting methods in manufacturing. It utilizes disposable models made of wax-like materials to manufacture complex parts with high precision. It is a versatile and highly efficient process that is particularly suited to the production of complex metal parts with high precision and minimal post-processing requirements.
Aluminum Investment Casting in Innovaw
Innovaw has three production lines for investment casting, including injection wax machines, wax storage tanks, dewaxing kettles, mold conveying lines, dewaxing ovens, recycling devices, PLC control system and other complete sets of equipment, as well as auxiliary equipment such as sand mixer, sand fall machine, shot blasting machine, molding machine and pouring machine.
Our investment casting products cover architectural hardware, aerospace, automotive parts, hydraulic equipment parts, agricultural machinery parts, sanitary hardware, tools and so on. The size of the products is from 50*50mm to 400*400mm, the weight is from 5g to 5Kg, and the daily output is 3-5 tons.
Material Scope:
Aluminum:
ASTM-A319, A413, A355, A356, A357
JIS-AC2B, AC4D, AC4C, AC3A, AC4A
DIN-AlSi7cu4, AlSi5cu1Mg, AlSi7Mg, AlSi12, AlSi9Mg, AlSi12Cu2Mg1, AlSi6Cu4
ENAC-45000, 45300, 42100, 44100, 43300
In order to better provide one-stop service to our customers, Innovaw continues to maintain a high investment in research and development in the field of investment casting.
We will continue to introduce industry advanced investment casting equipment. We continue to improve the details of our investment casting process in practice, pursuing every ounce of progress.
We continue to study the material properties and the best application of different materials in the field of investment casting.
What Is Investment Casting?
Investment casting, also known as lost wax casting, is one of the most diverse casting methods in manufacturing. It utilizes disposable models made of wax-like materials to manufacture complex parts with high precision. It is a versatile and highly efficient process that is particularly suited to the production of complex metal parts with high precision and minimal post-processing requirements.
1. Overview of the process
- Pattern Creation: The process begins with the creation of a wax mold, which is an exact replica of the item to be cast. The pattern is usually made of wax because it is easily molded and then melted away. The wax mold is a replica of the final part geometry. A “master model” serves as a standard that can be reused in many casting cycles. Nowadays, engineers use advanced techniques such as 3D printing or die casting to manufacture patterns.
- Wax Mold Assembly and Formation: Multiple models are assembled into a single investment casting mold, and the combined pattern is called a “tree”. The operator then applies a layer of refractory material to the model to obtain the desired characteristics. The tree is repeatedly dipped into a bath of ceramic slurry and sand mortar in a gradual rotating manner. Through several such dipping cycles, the thickness of the ceramic shell around the wax model increases. Eventually a shell is formed around it, which hardens to form the mold.
- Wax removal: After the ceramic shell is formed, the wax inside the shell is removed by melting, leaving a cavity in the shape of the desired part.
- Casting: Molten metal is then poured into the ceramic mold. The metal fills the cavity left by the wax and takes the shape of the original pattern.
- Cooling and Finishing: Once the metal has cooled and solidified, the ceramic shell is broken to reveal the cast metal part. The part may then undergo additional finishing processes to achieve the desired specifications.
2. Advantages of Investment Casting
Investment casting is a highly versatile manufacturing process that offers several significant advantages:
- High Precision and Tolerances: Investment casting is renowned for its ability to produce parts with tight tolerances and intricate designs. This process can handle complex geometries that would be challenging to achieve with other casting methods, making it ideal for applications requiring high precision.
- Excellent Surface Finish: The process yields a smooth surface finish, which often reduces the need for extensive machining after casting. This characteristic not only enhances the aesthetic quality of the final product but also minimizes additional labor and costs associated with finishing operations.
- Reduced Machining Requirements: One of the key benefits of investment casting is its ability to significantly reduce machining time. Because the process produces parts that are closer to the final shape, less material needs to be removed, leading to quicker lead times and lower production costs.
- Design Freedom: The investment casting process provides greater design freedom, allowing for the creation of complex shapes and features that would be difficult or impossible to achieve with traditional methods. This flexibility enables engineers and designers to innovate without being constrained by manufacturing limitations.
- Consistency and Repeatability: Investment casting offers a high degree of repeatability, which is crucial for mass production. Once a mold is created, it can be used to produce numerous identical parts, ensuring consistent quality across large production runs.
3. Applications of Investment Casting
Investment casting is a versatile manufacturing process that finds applications across a wide range of industries due to its precision and ability to produce complex geometries. Here are some key sectors where investment casting is commonly utilized:
- Aerospace Industry: Investment casting is extensively used in the aerospace sector for producing critical components such as engine parts, landing gear, and structural components. The process allows for the creation of lightweight yet strong parts that meet stringent safety and performance standards.
- Automotive Industry: In the automotive field, investment casting is employed to manufacture various components, including engine blocks, transmission cases, and suspension parts. The ability to produce intricate designs with high precision makes it ideal for modern automotive applications.
- Military and Defense: The military sector relies on investment casting for producing firearm components, missile parts, and other precision-engineered items. The durability and reliability of investment cast parts are crucial for defense applications.
- Marine Applications: Investment casting is also used in the marine industry for components such as propellers, pumps, and valves. The corrosion resistance of materials used in investment casting is particularly beneficial in harsh marine environments.
- Medical Devices: In the medical field, investment casting is utilized to create surgical instruments, implants, and other precision components. The high level of accuracy and the ability to produce complex shapes are essential for medical applications.
- Energy Sector: The energy industry, including oil and gas, power generation, and renewable energy, employs investment casting for components like **turbine blades and valve bodies**. The process is suitable for high-performance materials that can withstand extreme conditions.
Aluminum Investment Casting
Aluminum Investment Casting
Aluminum Investment Casting
Aluminum Investment Casting
Aluminum Investment Casting
Aluminum Investment Casting
Application Industry
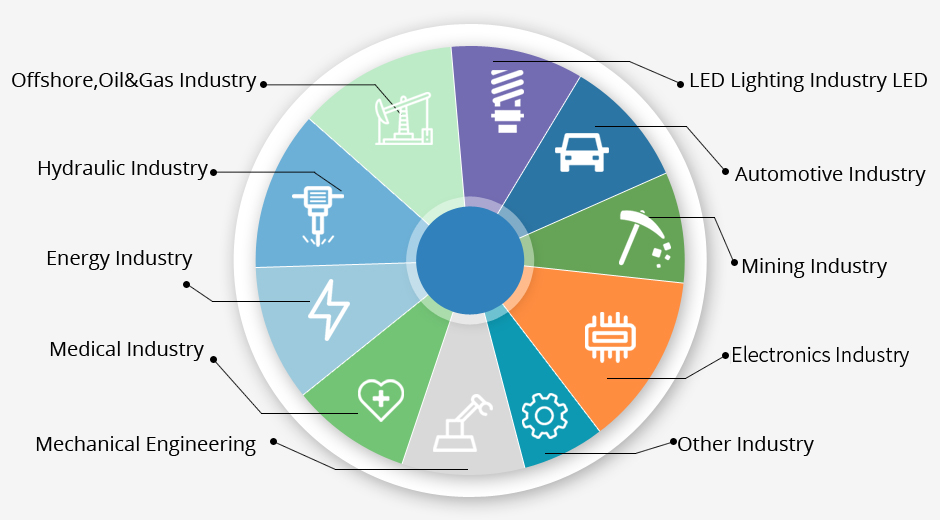
Partner
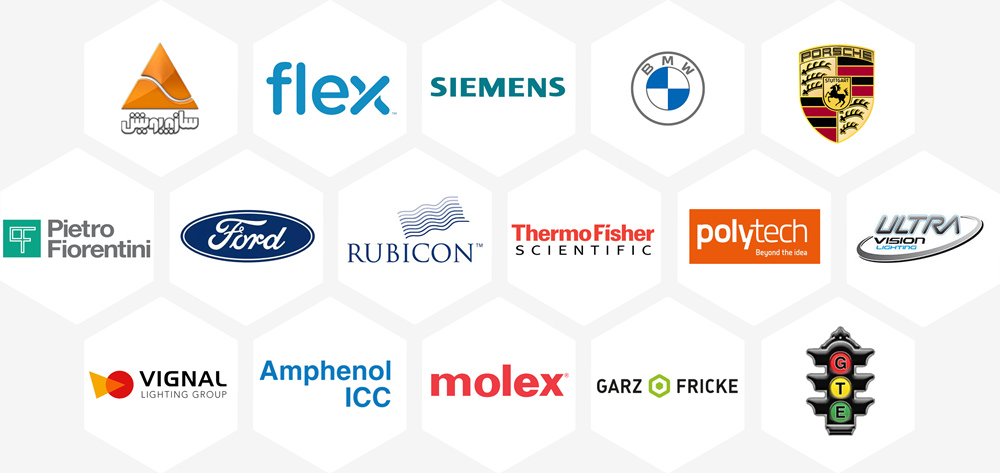