The high pressure zinc alloy die casting process is carried out in an automatic machine suitable for withstanding high pressure. The molten metal is pushed into a two-piece steel mold containing one or more cavities, each of which accurately replicates one or more parts in reverse. The mechanical properties of pressure zinc die castings are generally superior to other casting processes because of the rapid cooling and rapid solidification that occur when the molten metal comes into contact with the relatively cold steel side.
What are the advantages of zinc die casting?
When talking about the advantages of zinc die-casting, usually, other casting processes cannot be compared with zinc in terms of production time. There are a variety of casting processes that can be used to economically manufacture castings of the required size and quantity. However, the die casting productivity of zinc is much faster than aluminum or magnesium. Moreover, the casting tolerances of zinc alloys are smaller than any other metal or molded plastic. "Net shape" or "zero processing" manufacturing is the main advantage of zinc castings. The repeatability of smaller parts of zinc alloy die castings is less than ±0.001". Only a few other processes (such as aluminum die castings) can achieve the same net shape performance and eliminate machining.
Another great advantage of using zinc die castings is that zinc's excellent casting fluidity, strength and rigidity allow the design of thin-walled profiles, thereby reducing weight and saving material costs. INNOVAW handles all aspects of zinc alloy die castings, from mold design and testing to zinc component manufacturing, finishing and packaging. Zinc has excellent bearing and wear properties, can provide greater design flexibility and reduce manufacturing costs, so we can adopt the most complex design specifications and quickly and effectively transform them into finished products.
Zinc die castings in the automotive industry | Die casting applications in the industrial market
The zinc alloy die casting process is widely used in the construction and industrial fields to manufacture parts, but the most common application is in the automotive industry. In fact, automobiles have different parts that can be manufactured by die-casting processes, so much so that modern die-casting processes were first started in the automotive industry. The high strength and hardness of zinc make it suitable for many solutions and an ideal substitute for machining, pressing, stamping and manufacturing components. Many applications for zinc die casting manufacturing include:
-
Automotive interior beauty parts
-
Engine and other under-hood components
-
Power steering system
-
Brake parts and systems
-
Air conditioning components and systems
-
Fuel System
-
Intricate mesh shell
-
Electronic equipment
As mentioned earlier, the automotive industry is the most common application of zinc die castings. With the already impressive anti-corrosion properties of zinc die castings, INNOVAW is the leader in manufacturing high aesthetic quality and narrow tolerance zinc die castings.
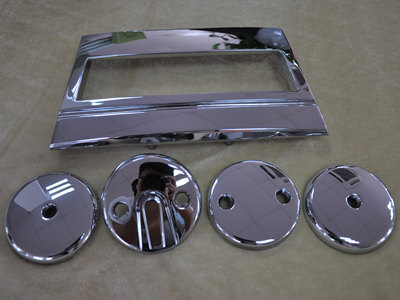
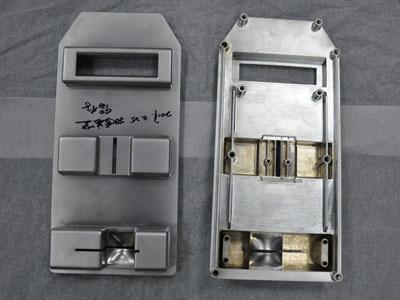
Application Industry
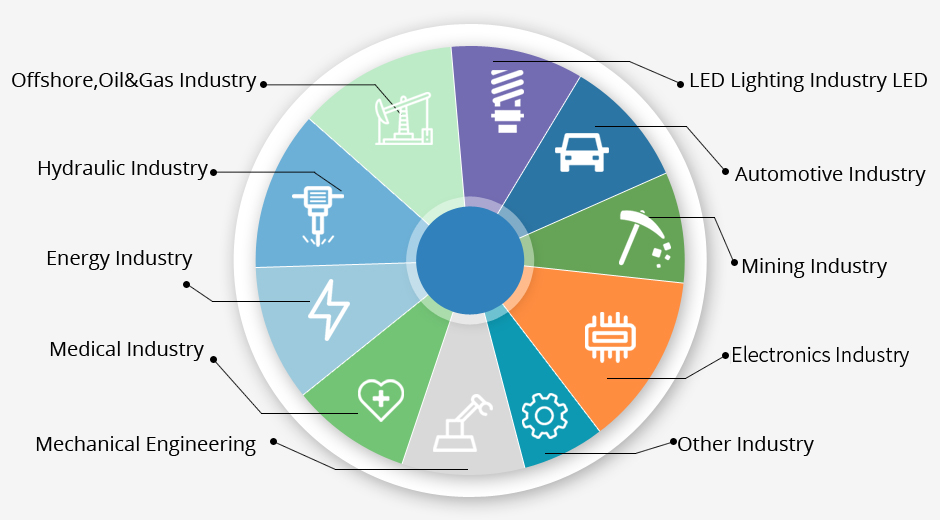
Partner
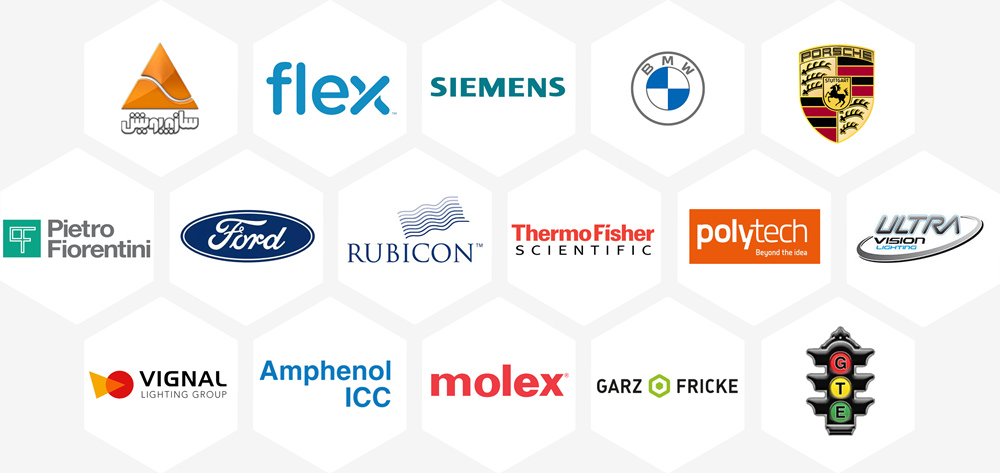